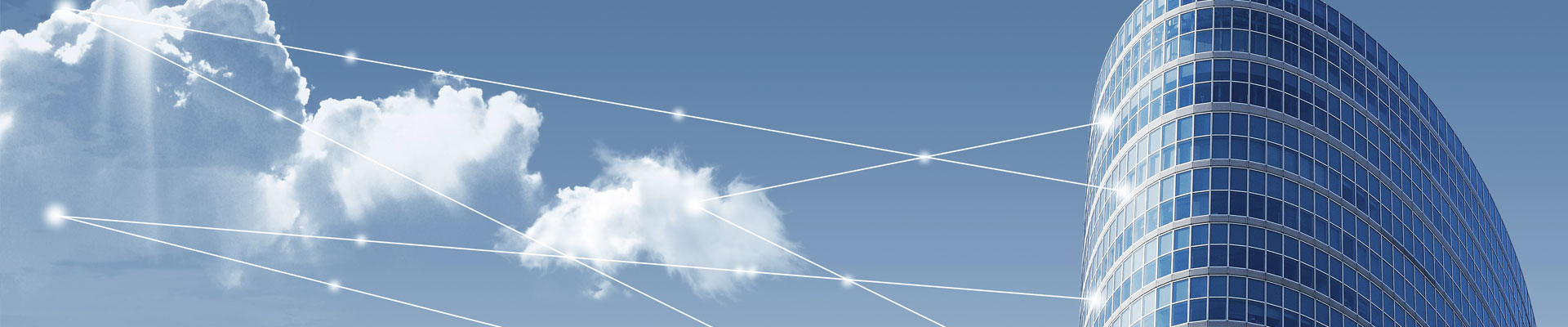

DFM审查对PCBA代工的重要性
在电子产品迭代加速的市场环境下,企业选择PCBA代工服务时往往关注两个核心指标:交付周期和产品良率。80%的生产异常都源于设计环节的工艺疏漏,这正是DFM(可制造性设计审查)成为行业必备流程的根本原因。
制造前哨站:DFM审查的本质解析
不同于常规的设计验证,DFM审查是连接研发与制造的工艺桥梁。该流程要求工程师同时具备电路设计能力和产线实操经验,从以下三个维度进行专业评估:
1. 工艺匹配度验证:对照SMT设备精度(±0.025mm)、回流焊温区设置等实际参数,核查焊盘尺寸、元件间距等设计指标
2. 成本控制预判:通过BOM清单交叉分析,识别特殊封装元件、非标连接器等可能增加采购成本的非常规设计
3. 可维护性评估:预留测试点间距、模块化布局等设计要素的合理性审查
四维价值:DFM带来的制造提升
1. 缩短15%产品导入周期
通过前置化发现设计缺陷,避免生产中途的工程变更。某智能穿戴设备案例显示,经完整DFM审查的项目平均减少3次工程迭代。
2. 降低30%质量成本
系统性排查焊盘虚焊、高频干扰等117项工艺风险点,将量产直通率提升至99.2%以上。
3. 优化20%物料成本
元件替代方案建议可降低BOM清单中15-20%的特殊器件采购需求,同时优化拼板方案提升板材利用率。
4. 延长产品生命周期
通过热力学仿真提前识别散热瓶颈,使工业控制设备MTBF(平均无故障时间)提升至50000小时。
专业服务商的DFM实施框架
阶段一:基础规范核查
- 元件间距≥0.3mm(0201封装)
- 焊盘尺寸公差±0.1mm
- 拼板V-CUT位置避让规则
阶段二:工艺可行性验证
- 双面回流焊器件重量比核算
- 通孔器件与SMD元件距离规划
- 治具开孔避位审查
阶段三:可靠性模拟
- 热应力分布仿真
- 机械振动测试预判
- 电流承载能力计算
阶段四:成本优化提案
- 等效元件替代方案
- 标准化元件库推荐
- 工艺路线优化建议
阶段五:量产风险预警
- 钢网开孔方案确认
- 红胶工艺适用性判断
- 检测工装适配性验证
行业趋势:DFM已成为制造能力分水岭
随着电子元器件微型化(01005封装应用)和高密度互联(HDI板)趋势加剧,缺乏DFM能力的代工厂正面临三大困境:
1. 无法承接BGA间距<0.4mm的高精度订单
2. 难以处理20层以上高多层板加工
3. 应对高频高速电路设计力不从心
制造前哨站:DFM审查的本质解析
不同于常规的设计验证,DFM审查是连接研发与制造的工艺桥梁。该流程要求工程师同时具备电路设计能力和产线实操经验,从以下三个维度进行专业评估:
1. 工艺匹配度验证:对照SMT设备精度(±0.025mm)、回流焊温区设置等实际参数,核查焊盘尺寸、元件间距等设计指标
2. 成本控制预判:通过BOM清单交叉分析,识别特殊封装元件、非标连接器等可能增加采购成本的非常规设计
3. 可维护性评估:预留测试点间距、模块化布局等设计要素的合理性审查
四维价值:DFM带来的制造提升
1. 缩短15%产品导入周期
通过前置化发现设计缺陷,避免生产中途的工程变更。某智能穿戴设备案例显示,经完整DFM审查的项目平均减少3次工程迭代。
2. 降低30%质量成本
系统性排查焊盘虚焊、高频干扰等117项工艺风险点,将量产直通率提升至99.2%以上。
3. 优化20%物料成本
元件替代方案建议可降低BOM清单中15-20%的特殊器件采购需求,同时优化拼板方案提升板材利用率。
4. 延长产品生命周期
通过热力学仿真提前识别散热瓶颈,使工业控制设备MTBF(平均无故障时间)提升至50000小时。
专业服务商的DFM实施框架
阶段一:基础规范核查
- 元件间距≥0.3mm(0201封装)
- 焊盘尺寸公差±0.1mm
- 拼板V-CUT位置避让规则
阶段二:工艺可行性验证
- 双面回流焊器件重量比核算
- 通孔器件与SMD元件距离规划
- 治具开孔避位审查
阶段三:可靠性模拟
- 热应力分布仿真
- 机械振动测试预判
- 电流承载能力计算
阶段四:成本优化提案
- 等效元件替代方案
- 标准化元件库推荐
- 工艺路线优化建议
阶段五:量产风险预警
- 钢网开孔方案确认
- 红胶工艺适用性判断
- 检测工装适配性验证
行业趋势:DFM已成为制造能力分水岭
随着电子元器件微型化(01005封装应用)和高密度互联(HDI板)趋势加剧,缺乏DFM能力的代工厂正面临三大困境:
1. 无法承接BGA间距<0.4mm的高精度订单
2. 难以处理20层以上高多层板加工
3. 应对高频高速电路设计力不从心
选择具有深度DFM实施能力的PCBA服务商,意味着在产品设计阶段就植入了量产成功基因。这种设计与制造的深度协同,正是保障电子产品从样品到批量生产顺利过渡的核心竞争力。
英特丽集团具有3大ODM开发中心,工程师100+。OEM工厂SMT线体全部采用进口一线西门子、松下等品牌设备,同时采用智能工厂(ERP\MES\WMS)生产管理模式; 并通过ISO90001、ISO14000、IATF16949、ISO13485等各项体系认证;公司重点业务方向聚焦汽车电子、新能源、医疗电子、军工、工控、物联网、部分消费类等产品;公司规划五座生产基地,2025年达成150条SMT产线规模;目前,江西、安徽、山西、四川、湖北五个智造基地已初具规模;我们目标把英特丽电子打造成一站式ODM+EMS智造服务行业标杆。
上一篇: 什么是SMT开机费?如何减免或优化? 下一篇: PCBA焊接回流焊与波峰焊两种工艺的选择
Copyright © 2020-2022 赣ICP备19014000号-1
赣公网安备36100002000168号 江西英特丽电子科技股份有限公司深圳分公司
