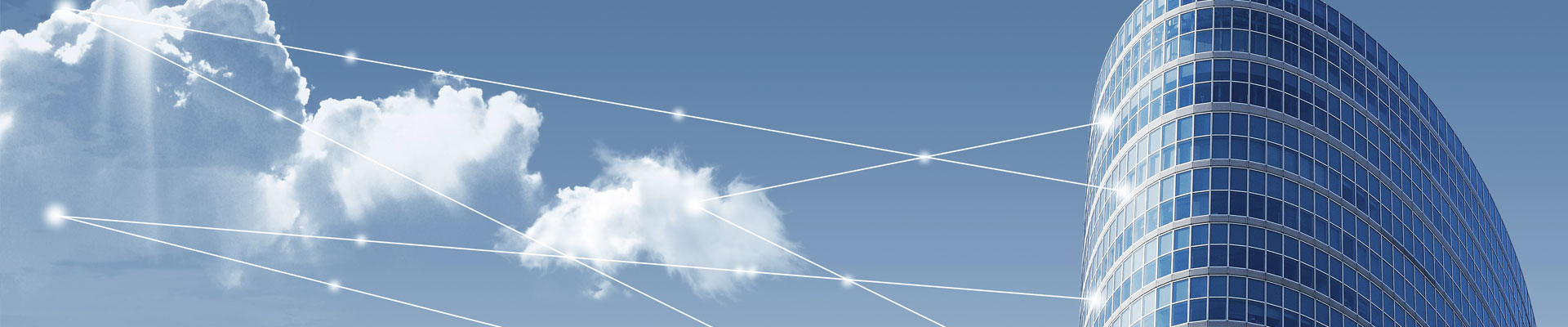

PCBA打样全流程的六大环节
PCBA打样是电子产品研发过程中的重要环节,涉及从设计到成品交付的多个流程。为了确保产品性能稳定、符合设计预期,与PCBA代工厂的高效协作至关重要。本文将详细解析PCBA打样的全流程,帮助电子产品设计师了解每个环节的具体流程与注意事项。
一、需求沟通:明确产品设计与生产目标
1. 提交产品设计资料
设计师需向PCBA代工厂提供完整的设计资料,包括:
- OM清单(物料清单): 标明元器件型号、数量及规格。
- 电路原理图与PCB文件: 包含布局与布线设计。
- 工艺要求: 包括焊接方式、丝印标记等。
- 测试要求: 需要进行的功能性与可靠性测试标准。
2. 技术评审与方案确认
代工厂工程师与设计师进行技术评审,检查设计的可制造性(DFM)、元件可采购性(DFA),并确认生产与测试方案,避免潜在设计缺陷。
二、PCB设计与生产:基础硬件的构建
1. PCB设计优化
如客户需要,代工厂可提供PCB设计优化服务,改善电路布局、信号完整性及散热性能,提升产品可靠性。
2. PCB制造与检查
根据设计文件,生产PCB板,主要工艺包括:
- 切割与钻孔: 根据层数与尺寸加工PCB板材。
- 铜箔电镀与蚀刻: 完成电路导通层的制作。
- 丝印与表面处理: 标记元件位置,防止氧化。
完成PCB制造后,进行光学检测(AOI)和电气测试,确保PCB符合设计要求。
三、元件采购:确保物料及时可靠
元件采购是PCBA打样中关键环节,影响生产周期与成本。
1. 物料清单(BOM)管理
- 元件选型确认: 确保物料规格与设计匹配。
- 供应链管理: 选择正规供应商,确保物料品质与供货稳定性。
2. 来料检验(IQC)
采购到的元器件需经过严格的来料检验,包括外观检查、电性能测试等,杜绝劣质元件。
四、SMT贴片与DIP插件:元件组装核心工艺
1. SMT贴片工艺
- 钢网印刷: 在PCB上印刷锡膏,保证焊点连接良好。
- 贴片机装配: 自动将贴片元件安装在PCB板上。
- 回流焊接: 在高温回流焊炉中完成元件焊接。
2. DIP插件工艺(如适用)
- 手工或自动插件,将较大的通孔元件插入PCB。
- 波峰焊接工艺实现焊点固定,确保焊接牢固。
五、焊接与装配:电路连接与整体结构完成
1. 手工焊接与修整
对特殊元件进行手工焊接与修补,确保所有焊点可靠。
2. 电气与功能测试
- ICT在线测试: 测试电路连接与基本功能。
- 功能测试(FCT): 模拟实际使用场景,确保产品正常工作。
六、质量检测与产品交付:确保最终成品可靠
1. 出厂质检(OQC)
- 外观检查: 确保PCB板清洁、无焊接缺陷。
- 电气性能测试: 确保功能与设计一致。
2. 包装与交付
一、需求沟通:明确产品设计与生产目标
1. 提交产品设计资料
设计师需向PCBA代工厂提供完整的设计资料,包括:
- OM清单(物料清单): 标明元器件型号、数量及规格。
- 电路原理图与PCB文件: 包含布局与布线设计。
- 工艺要求: 包括焊接方式、丝印标记等。
- 测试要求: 需要进行的功能性与可靠性测试标准。
2. 技术评审与方案确认
代工厂工程师与设计师进行技术评审,检查设计的可制造性(DFM)、元件可采购性(DFA),并确认生产与测试方案,避免潜在设计缺陷。
二、PCB设计与生产:基础硬件的构建
1. PCB设计优化
如客户需要,代工厂可提供PCB设计优化服务,改善电路布局、信号完整性及散热性能,提升产品可靠性。
2. PCB制造与检查
根据设计文件,生产PCB板,主要工艺包括:
- 切割与钻孔: 根据层数与尺寸加工PCB板材。
- 铜箔电镀与蚀刻: 完成电路导通层的制作。
- 丝印与表面处理: 标记元件位置,防止氧化。
完成PCB制造后,进行光学检测(AOI)和电气测试,确保PCB符合设计要求。
三、元件采购:确保物料及时可靠
元件采购是PCBA打样中关键环节,影响生产周期与成本。
1. 物料清单(BOM)管理
- 元件选型确认: 确保物料规格与设计匹配。
- 供应链管理: 选择正规供应商,确保物料品质与供货稳定性。
2. 来料检验(IQC)
采购到的元器件需经过严格的来料检验,包括外观检查、电性能测试等,杜绝劣质元件。
四、SMT贴片与DIP插件:元件组装核心工艺
1. SMT贴片工艺
- 钢网印刷: 在PCB上印刷锡膏,保证焊点连接良好。
- 贴片机装配: 自动将贴片元件安装在PCB板上。
- 回流焊接: 在高温回流焊炉中完成元件焊接。
2. DIP插件工艺(如适用)
- 手工或自动插件,将较大的通孔元件插入PCB。
- 波峰焊接工艺实现焊点固定,确保焊接牢固。
五、焊接与装配:电路连接与整体结构完成
1. 手工焊接与修整
对特殊元件进行手工焊接与修补,确保所有焊点可靠。
2. 电气与功能测试
- ICT在线测试: 测试电路连接与基本功能。
- 功能测试(FCT): 模拟实际使用场景,确保产品正常工作。
六、质量检测与产品交付:确保最终成品可靠
1. 出厂质检(OQC)
- 外观检查: 确保PCB板清洁、无焊接缺陷。
- 电气性能测试: 确保功能与设计一致。
2. 包装与交付
产品通过最终检查后,按照客户要求进行包装与交付,确保安全运输与及时交货。
英特丽集团具有3大ODM开发中心,工程师100+。OEM工厂SMT线体全部采用进口一线西门子、松下等品牌设备,同时采用智能工厂(ERP\MES\WMS)生产管理模式; 并通过ISO90001、ISO14000、IATF16949、ISO13485等各项体系认证;公司重点业务方向聚焦汽车电子、新能源、医疗电子、军工、工控、物联网、部分消费类等产品;公司规划五座生产基地,2025年达成150条SMT产线规模;目前,江西、安徽、山西、四川、湖北五个智造基地已初具规模;我们目标把英特丽电子打造成一站式ODM+EMS智造服务行业标杆。
上一篇: 选择国内SMT贴片加工厂的五大优势 下一篇: 判断PCBA工厂可靠性的三个关键方面
Copyright © 2020-2022 赣ICP备19014000号-1
赣公网安备36100002000168号 江西英特丽电子科技股份有限公司深圳分公司
