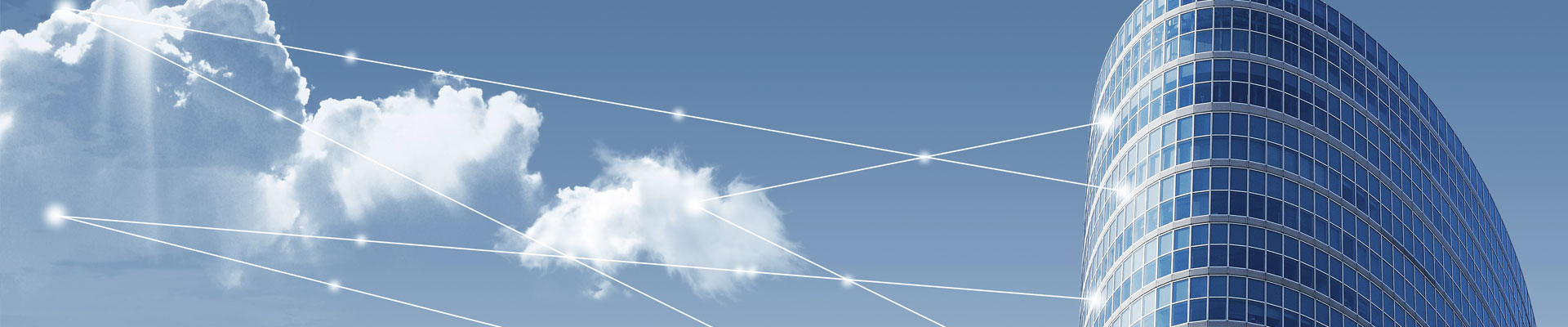

导致SMT打样费用高的主要原因
表面贴装技术(SMT)已成为现代电子制造的核心工艺之一。然而,许多企业和工程师在进行SMT打样时,常常发现其费用相对较高。接下来带大家分析下导致SMT打样费用高的主要原因,以帮助企业和设计人员更好地理解成本结构,并在打样过程中做出更明智的决策。
1. 小批量生产的成本分摊
SMT打样通常涉及小批量生产,而生产线的启动成本、设备调试、材料准备等固定成本不因生产量的减少而降低。由于打样批量较小,这些固定成本无法被大量产品分摊,导致单位产品的成本较高。此外,生产线的频繁切换和调整也增加了运营成本。
2. 设备和工艺的高要求
SMT设备如贴片机、回流焊、AOI检测设备等价格昂贵,且需要定期维护和校准。为了保证样品的高质量,SMT打样通常要求使用高精度的设备和工艺,这无形中增加了打样的成本。例如,某些微型元器件的贴装精度要求极高,需要采用专门的高精度贴片机,这种设备的使用和维护成本都较高。
3. 元器件采购的高成本
在SMT打样过程中,由于样品数量有限,元器件的采购成本通常较高。供应商对于小批量采购通常没有优惠,而部分特殊元器件还可能存在最小订购量要求,导致单个样品的元器件成本攀升。此外,为了确保样品质量,打样过程中通常选用高品质的元器件,这进一步增加了成本。
4. 人工成本的影响
SMT打样不仅依赖于自动化设备,还需要大量的手工操作,如PCB文件的准备、物料的准备与摆放、设备的调试、样品的检测与返工等。由于样品生产的复杂性和高要求,这些手工操作通常由经验丰富的技术人员完成,其人工成本较高。
5. 定制化服务的成本
SMT打样往往需要定制化服务,如多次设计更改、特殊工艺要求、快速交货等。为了满足客户的这些个性化需求,制造商需要投入额外的资源和时间,进一步推高了打样的费用。
6. 质量检测和返工成本
打样阶段的质量检测要求非常严格,往往需要多次检测和返工。使用AOI(自动光学检测)设备、X-Ray检测、功能测试等手段来确保样品的质量,这些检测设备的使用和返工过程的成本不容忽视。此外,打样过程中发现的设计问题或工艺缺陷可能需要进行多次返工,进一步增加了费用。
结论
1. 小批量生产的成本分摊
SMT打样通常涉及小批量生产,而生产线的启动成本、设备调试、材料准备等固定成本不因生产量的减少而降低。由于打样批量较小,这些固定成本无法被大量产品分摊,导致单位产品的成本较高。此外,生产线的频繁切换和调整也增加了运营成本。
2. 设备和工艺的高要求
SMT设备如贴片机、回流焊、AOI检测设备等价格昂贵,且需要定期维护和校准。为了保证样品的高质量,SMT打样通常要求使用高精度的设备和工艺,这无形中增加了打样的成本。例如,某些微型元器件的贴装精度要求极高,需要采用专门的高精度贴片机,这种设备的使用和维护成本都较高。
3. 元器件采购的高成本
在SMT打样过程中,由于样品数量有限,元器件的采购成本通常较高。供应商对于小批量采购通常没有优惠,而部分特殊元器件还可能存在最小订购量要求,导致单个样品的元器件成本攀升。此外,为了确保样品质量,打样过程中通常选用高品质的元器件,这进一步增加了成本。
4. 人工成本的影响
SMT打样不仅依赖于自动化设备,还需要大量的手工操作,如PCB文件的准备、物料的准备与摆放、设备的调试、样品的检测与返工等。由于样品生产的复杂性和高要求,这些手工操作通常由经验丰富的技术人员完成,其人工成本较高。
5. 定制化服务的成本
SMT打样往往需要定制化服务,如多次设计更改、特殊工艺要求、快速交货等。为了满足客户的这些个性化需求,制造商需要投入额外的资源和时间,进一步推高了打样的费用。
6. 质量检测和返工成本
打样阶段的质量检测要求非常严格,往往需要多次检测和返工。使用AOI(自动光学检测)设备、X-Ray检测、功能测试等手段来确保样品的质量,这些检测设备的使用和返工过程的成本不容忽视。此外,打样过程中发现的设计问题或工艺缺陷可能需要进行多次返工,进一步增加了费用。
结论
SMT打样费用高的原因主要源于小批量生产无法摊销固定成本、高要求的设备和工艺、元器件采购的高成本、人工成本、定制化服务需求以及严格的质量检测和返工成本等多个因素。理解这些成本构成有助于企业在SMT打样时做出更具成本效益的决策,并在设计和工艺优化中寻找降低成本的方法。
英特丽集团具有3大ODM开发中心,工程师100+。OEM工厂SMT线体全部采用进口一线西门子、松下等品牌设备,同时采用智能工厂(ERP\MES\WMS)生产管理模式; 并通过ISO90001、ISO14000、IATF16949、ISO13485等各项体系认证;公司重点业务方向聚焦汽车电子、新能源、医疗电子、军工、工控、物联网、部分消费类等产品;公司规划五座生产基地,2025年达成150条SMT产线规模;目前,江西、安徽、山西、四川、湖北五个智造基地已初具规模;我们目标把英特丽电子打造成一站式ODM+EMS智造服务行业标杆。
Copyright © 2020-2022 赣ICP备19014000号-1
赣公网安备36100002000168号 江西英特丽电子科技股份有限公司深圳分公司
