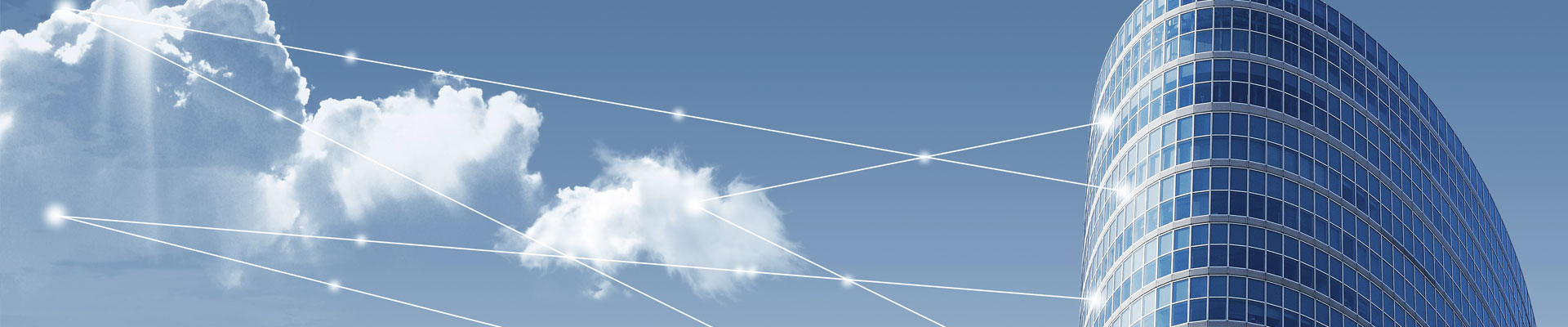

英特丽SMT贴片加工使用拼版的限制
将电路板(PCB)拼板(panelize)成【阴阳板或鸳鸯板(Mirror Board)】,虽然可以增加SMT贴片加工产线的效率,也有节省材料成本的优势,可是这两种【阴阳板】的设计却有其各自的缺点及限制,本文就来探讨并寻求其解决之道。
关于「正反面颠倒的阴阳板」,其限制是不建议使用于有较重零件的板子上面,因为较重零件一般会放在第二面才打件,这样可以避免较重零件过第二次回焊炉(reflow oven)时锡膏重新熔融而掉落的风险。
方法一:可以在较重的零件下点胶(dispense),早期的SMT线,点红胶制程及点胶机是必要的设备,因为点过胶的零件可以拿去过波峰焊(wave soldering),现在的SMT线就不一定有这个设备了。 如果没有,也可以考虑用手点胶,但个人不建议,因为人工操作质量较难管控。
方法二:使用载具(carrier)。 过回焊炉载具可以设计成刚好支撑住较重的零件,这样较重零件过二次回流焊时就不易掉落。 但是一个载具的费用不便宜,而且载具全部数量排起来要大于回焊炉(reflow oven)的长度,也就是要计算回焊炉内同时有多少片板子行走期间,还要加上备品(buffer),全部加起来没有三十个也要二十个以上,所费不眦。 另外载具因为需要承受多次重复经过回流焊的高温,所以一般会采用金属材质或特殊耐高温的塑料制成。 还有一点需要特别提醒,使用Carrier会需要多一个人工成本,把板子放到Carrier上面也要人工啊。
方法三:手焊较重零件。 个人不建议此法,原因还是人工不易控制质量,而且有些零件不易手焊。
另外对于「正反面颠倒的阴阳板」还有一个问题,就是有些板子可能在某一面使用了容易吸热的零件(如大面积的ATM读卡槽),这些零件需要较长的升温时间以达到锡膏的熔融温度,但又不可以烧伤(burn)其他较脆弱的零件。 这种板子需要特别留意回焊温度曲线(Reflow Profile)的调整。
至于「同一面上下颠倒的阴阳板」,基本上对SMT线效率的帮助不大,但它可以达到节省板材的目的,如何裁切板边是只这种拼板需要考虑的问题。 正常的拼板,通常可以采用V-Cut的方式来裁切板边,比较省Cost,但拼成阴阳板就有所限制了,因为V-Cut只能作全直线切割,弯曲的板边就要靠Router机了,详细可以参考 电路板去板边 ─ V-Cut 分板机 一文。
拼板之后容易有Cross Board (打X板)产生,而且板子拼得越多,X-board 的机会就越多。 X-board是板厂制程中必然会出现的产物,所谓X-board 就是拼板中有一片以上的不良板子,一般板厂会在坏板上用签字笔打一个X,故称之为X-board。 大部分的SMT打件工厂都不希望接受这种板子,因为会造成效率的损失,但这种电路板在制程中又无法绝对避免,所以连板数越多,电路板厂报废的数量就会越多,相对的成本也就提高。 所以电路板厂商会希望连板的数目越少越好,因为这样可以避免掉X-board的损失,当然羊毛还是出在羊身上,如果板厂一直无法克服X-board的损失,最后价钱还是会反应到客户的身上。
关于「正反面颠倒的阴阳板」,其限制是不建议使用于有较重零件的板子上面,因为较重零件一般会放在第二面才打件,这样可以避免较重零件过第二次回焊炉(reflow oven)时锡膏重新熔融而掉落的风险。
方法一:可以在较重的零件下点胶(dispense),早期的SMT线,点红胶制程及点胶机是必要的设备,因为点过胶的零件可以拿去过波峰焊(wave soldering),现在的SMT线就不一定有这个设备了。 如果没有,也可以考虑用手点胶,但个人不建议,因为人工操作质量较难管控。
方法二:使用载具(carrier)。 过回焊炉载具可以设计成刚好支撑住较重的零件,这样较重零件过二次回流焊时就不易掉落。 但是一个载具的费用不便宜,而且载具全部数量排起来要大于回焊炉(reflow oven)的长度,也就是要计算回焊炉内同时有多少片板子行走期间,还要加上备品(buffer),全部加起来没有三十个也要二十个以上,所费不眦。 另外载具因为需要承受多次重复经过回流焊的高温,所以一般会采用金属材质或特殊耐高温的塑料制成。 还有一点需要特别提醒,使用Carrier会需要多一个人工成本,把板子放到Carrier上面也要人工啊。
方法三:手焊较重零件。 个人不建议此法,原因还是人工不易控制质量,而且有些零件不易手焊。
另外对于「正反面颠倒的阴阳板」还有一个问题,就是有些板子可能在某一面使用了容易吸热的零件(如大面积的ATM读卡槽),这些零件需要较长的升温时间以达到锡膏的熔融温度,但又不可以烧伤(burn)其他较脆弱的零件。 这种板子需要特别留意回焊温度曲线(Reflow Profile)的调整。
至于「同一面上下颠倒的阴阳板」,基本上对SMT线效率的帮助不大,但它可以达到节省板材的目的,如何裁切板边是只这种拼板需要考虑的问题。 正常的拼板,通常可以采用V-Cut的方式来裁切板边,比较省Cost,但拼成阴阳板就有所限制了,因为V-Cut只能作全直线切割,弯曲的板边就要靠Router机了,详细可以参考 电路板去板边 ─ V-Cut 分板机 一文。
拼板之后容易有Cross Board (打X板)产生,而且板子拼得越多,X-board 的机会就越多。 X-board是板厂制程中必然会出现的产物,所谓X-board 就是拼板中有一片以上的不良板子,一般板厂会在坏板上用签字笔打一个X,故称之为X-board。 大部分的SMT打件工厂都不希望接受这种板子,因为会造成效率的损失,但这种电路板在制程中又无法绝对避免,所以连板数越多,电路板厂报废的数量就会越多,相对的成本也就提高。 所以电路板厂商会希望连板的数目越少越好,因为这样可以避免掉X-board的损失,当然羊毛还是出在羊身上,如果板厂一直无法克服X-board的损失,最后价钱还是会反应到客户的身上。
其实有些专业的SMT贴片加工厂会以人工手动的方式后制拼板,但需要用到一些技巧,也不得不佩服这些厂商的点子。
江西英特丽电子科技有限公司成立于2016年5月,坐落于人杰地灵的才子之乡-江西省抚州市临川区,江西英特丽电子科技有限公司现有30,000平方米的厂房面积,24条SMT产线,8条插件线,4条波峰焊线,8条组装线,4条包装线,总投资10个亿,配备先进完善的数字化管理体系,致力于打造工业4.0智慧工厂。
上一篇: 英特丽smt贴片加工时机器常见故障分析 下一篇: 英特丽SMT贴片加工技术深度解读
Copyright © 2020-2022 赣ICP备19014000号-1
赣公网安备36100002000168号 江西英特丽电子科技股份有限公司深圳分公司
