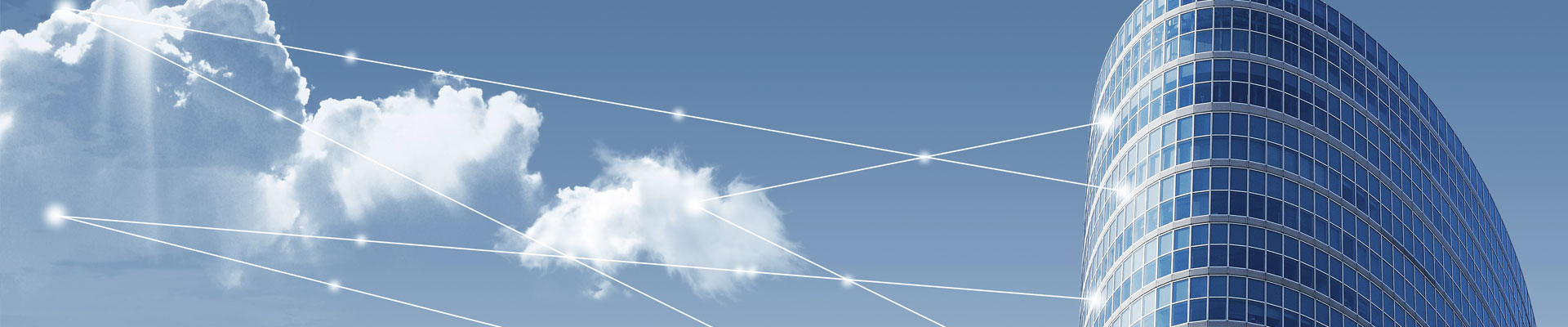

英特丽SMT贴片加工技术深度解析
SMT(英文:Surface-mount technology),即表面贴装技术,是一种将元器件贴装或直接放置在印刷电路板表面的电子线路生产技术。在SMT贴片加工行业,有SMD(surface-mount device,表面贴装器件)和THT(through-hole technology穿孔插装技术)两种方法。两种技术可以在同一块PCB板上应用,只不过穿孔插装技术应用在哪些不适合表面贴装的元器件(比如大的变压器、连接器、电解电容等)。SMT元件通常比穿孔插装元件小,因为它的引脚更小甚至是没有引脚,它可能是各种类型、接触方式的短脚或者短引线,或者是球状矩阵排列(BGA)等。
SMT历史
表面贴装技术起源于60年代,最初由美国IBM公司进行技术研发,之后于80年代后期渐趋成熟。起初被IBM在1960年设计应用于一款小型电脑中,这款电脑后来被作为土星IB和土星五号运载火箭的仪器组件。元器件被重新进行机械设计,具有极小的金属分页或端盖,以至于可以直接焊接到PCB表面。元器件变得更小,并在PCB板的两面采用表面方式进行元器件的贴装,从而替代穿孔插装方式,允许更高的线路密度。通常只有焊接连接处将器件固定在板上,在极少情况下,如果一些元器件很大或者很重的时候,需在另外一面使用一些粘合剂防止元器件在回流焊的时候脱落。如果SMT贴片加工和穿孔插装工艺同时进行时,粘合剂有些时候被用作将另一面的SMT元件的固定。在替代方式下,SMT和穿孔插装元件可以一起焊接,无须借助粘合剂,如果SMT元件是第一次经过回流焊的话,从而选择性的焊接涂层将用作在回流焊过程中阻止元件的焊接以及元件在波峰焊接时浮动。表面贴装本身引领一定程度上的自动化,减少人工成本并且显著提升生产效率。SMD元件的大小和重量只有穿孔插装元件的1/4到1/10,并且成本只有1/2到1/4。
SMT术语
因为表面贴装是一种生产科技,因而有很多不同的术语,尤其是当处于不同生产环境中时,需要显著区分一些生产的元件、科技、设备。主要包含如下表格中的术语:
术语 解释
SMD:表面贴装元件(主动、被动以及机电元件)
SMT:表面贴装技术(组装和焊接技术)
SMA:表面组装工艺(使用SMT模块化组装)
SMC:表面贴装元件(即用于SMT的元件)
SMP:表面贴装封装(SMD元件的封装方式)
SME:表面贴装设备(SMT组装设备等)
SMT表面贴装技术
smt生产线需要表面贴装元器件的位置都需要平整,通常焊锡、沉银或者沉金并没有通孔的焊接位置被称为“焊盘”。锡膏,一种由铅锡成分和助焊混合物组成具有粘性的物质,借助锡膏印刷机,渗透过不锈钢或镍制钢网附着到焊盘上,也可通过喷印原理来完成,类似于喷墨打印机。锡膏印刷完毕后,电路板将经过拾取和放置设备,通过相应的传送带进行贴装。将要被贴装的元器件一般放置在纸质或塑料的管道中,并借助飞达安装在SMT贴片机器上。一些个头比较大的集成电路将通过防静电托盘传送。SMT设备从飞达中取出相应的元器件并将其贴装到PCB上,由于PCB上的锡膏具有一定的粘性,因而在焊盘上的元器件有很好的附着效应。
此时,PCB板将被传送至回流焊锡炉中。回流焊先头拥有一个预热区,电路板和元器件的温度逐渐上升,然后进入高温区,锡膏会融化并绑定焊盘和元器件,融化的锡膏表面张力会让元器件保留在所处位置,不发生偏移,甚至该表面张力会自动将略有偏位的元器件拉回到正确位置。回流焊接技术有很多种,一种是使用红外灯(被称为红外回流焊),另一种是使用热气对流,还有一种是最为流行的技术,便是采用特殊的高沸点碳氟化合物液体(被称为蒸汽回流焊)。鉴于环境考虑,这种技术在无铅法规出台后,逐渐放弃。2008年之前,采用标准空气或者氮气对流回流焊是主流。每种方法都有其优劣势。红外照射方式,板设计者必须注意:短元器件不会被高的元件所遮挡,但是如果设计者知道生产过程中使用蒸汽回流焊或者对流回流焊的话,元件位置便不会是需要考虑的因素。在回流焊阶段,一些非常规或者热敏感元器件需要手工焊接,但对于大量的这种元件,就需要通过红外光束或者对流设备来完成相应的回流焊接工艺。
如果PCB板是双面设计,那么所有的锡膏印刷、贴装和回流焊过程需要重复一次,通过锡膏或者红胶将元件粘附在指定位置。如果需要机型波峰焊工艺,元件需要借助红胶进行粘附,以防止元件在波峰焊受热过程中由于焊锡融化而造成的脱落。
完成焊接过程后,板面需要经过清洗,以去除松香助焊剂以及一些锡球,防止他们造成元件之间的短路。松香助焊剂通过碳氟化合物溶剂、高燃点碳氢化合物溶剂或者低燃点溶剂(比如从橙皮中提取的柠檬油精)进行清除。水溶性助焊剂通过离子水和清洁剂清除,然后利用风刀快速移除表面水分。但是,绝大不分的贴装执行无清洗过程,即松香助焊剂将留在PCB板的表面,这将节约清洗成本、提高生产效率、减少浪费。
一些SMT贴装生产标准,比如IPC(Association Connecting Electronics Industries)需要执行清洗标准,以便确保PCB板的清洁,甚至一些无须清理的助焊剂也必须被清除。正确的清晰将清理掉线路之间的肉眼无法识别的助焊剂、脏污和杂质等。但是,并不是所有厂商会严格遵从IPC标准并显示在板面上,或者客户根本不在意。事实上,很多厂家的制作标准是比IPC标准更加的严格。
最后,PCB板需要经过目检,查看是否元件漏贴、方向错误、虚焊、短路等。如果需要,有问题的板需要送至专业的返修台进行维修,比如经过ICT测试或者FCT功能测试环节,直至测试PCB板工作正常。
SMT优势
SMT相比传统的过孔插装技术具有如下主要优势:
(1)更小的元器件。2012年即实现0.4*0.2mm(0.016*0.008 in: 01005),并有更小型化的发展趋势
(2)更高的元件密度(单位面积内的元件数)以及单个元件更多的连接数
(3)更高的连接密度
(4)更低的成本和时间(上线生产)
(5)PCB设计和制作中更少的孔
(6)更加简单快速的贴装
(7)元件贴装中的微小错误会因为融化锡膏的表面张力自动拉伸修复
(8)元件可以在板的上下两面进行贴装焊接
(9)更低的电阻和电感效应,导致更少的RF信号效应
(10)在振动和跌落情况下更好的机械性能
(11)很多SMT元件相比插件元件要更加便宜
(12)更好的EMC性能,鉴于更小的电磁线圈从而产生更低的电磁辐射
SMT劣势
(1)因为更小尺寸和SMD引线间距,贴装或者元件层面的手工维修更加困难,需要专业熟练工人和更贵的返修工具进行操作
(2)SMD元件不能直接用于插入式母板(一种快速测试打样工具),需要定制一块PCB或者将SMD元件焊接到引脚载具上。
(3)SMD焊锡连接可能在热力循环中被灌注成分损坏
(4)SMT焊接连接处变得更小,间距越来越小,导致SMT工艺要求精度更高
(5)SMT不适于大体积、高能、高电压元件,例如电源电路中的变压器等,将SMT和插件工艺融合在一起,是比较常见的。
(6)SMT不适用于频繁机械应力的应用中,比如一些连接器,作为接口同外部连接,频发拔插对于焊接的稳定性提出了挑战
SMT返修
SMT贴片加工维修在整个PCBA加工工艺过程中,SMT问题元件经常采用电烙铁或者非接触式返修系统进行维修。在通常情况下,返修系统是更好的选择,因为SMD元件的维修需要相当熟练技能,并且不太容易。非接触式焊接返修方法:红外焊接和热气焊接。
红外方式
通过红外焊接方式,焊接处经过长短波的电磁感应而受热融化。优势有:
(1)建议安装
(2)无须加压空气
(3)无须针对不同元件的吸嘴,减少更换吸嘴的成本
(4)快速红外源的反应
劣势
(1)中央区域相比外围区域受热更多
(2)温度控制不够精确,极易达到峰值
(3)周围元件需要覆盖,避免损害,需要更多的时间
(4)表面温度取决于元件的反射率
(5)温度取决于表面形状,对流能量损耗将减少元件的温度
(6)没有回流氛围可能性
热气方式
在热气方式的焊接中,连接处的能量受热通过热气传输,通常借助空气或者氮气。优势
(1)模仿回流焊接中的场景
(2)一些系统允许在热空气和氮气中进行切换
(3)标准元件吸嘴,拥有更高的稳定性和快速处理过程
(4)允许可再生焊接
(5)足够的热能,大量元件均可以受热
(6)受热均匀
(7)元件受热温度不会超过设定的气体温度
(8)回流之后的快速冷却,导致更小的焊接纹路
劣势:热发生器的热力性能导致较慢的反应。返修通常能够更正一些由于人工或者机器引致的错误,包含如下步骤
融化焊锡并且移动元件
移动残余焊锡
直接或分发式印刷锡膏在PCB板上
贴装新的元件并回流焊
SMT历史
表面贴装技术起源于60年代,最初由美国IBM公司进行技术研发,之后于80年代后期渐趋成熟。起初被IBM在1960年设计应用于一款小型电脑中,这款电脑后来被作为土星IB和土星五号运载火箭的仪器组件。元器件被重新进行机械设计,具有极小的金属分页或端盖,以至于可以直接焊接到PCB表面。元器件变得更小,并在PCB板的两面采用表面方式进行元器件的贴装,从而替代穿孔插装方式,允许更高的线路密度。通常只有焊接连接处将器件固定在板上,在极少情况下,如果一些元器件很大或者很重的时候,需在另外一面使用一些粘合剂防止元器件在回流焊的时候脱落。如果SMT贴片加工和穿孔插装工艺同时进行时,粘合剂有些时候被用作将另一面的SMT元件的固定。在替代方式下,SMT和穿孔插装元件可以一起焊接,无须借助粘合剂,如果SMT元件是第一次经过回流焊的话,从而选择性的焊接涂层将用作在回流焊过程中阻止元件的焊接以及元件在波峰焊接时浮动。表面贴装本身引领一定程度上的自动化,减少人工成本并且显著提升生产效率。SMD元件的大小和重量只有穿孔插装元件的1/4到1/10,并且成本只有1/2到1/4。
SMT术语
因为表面贴装是一种生产科技,因而有很多不同的术语,尤其是当处于不同生产环境中时,需要显著区分一些生产的元件、科技、设备。主要包含如下表格中的术语:
术语 解释
SMD:表面贴装元件(主动、被动以及机电元件)
SMT:表面贴装技术(组装和焊接技术)
SMA:表面组装工艺(使用SMT模块化组装)
SMC:表面贴装元件(即用于SMT的元件)
SMP:表面贴装封装(SMD元件的封装方式)
SME:表面贴装设备(SMT组装设备等)
SMT表面贴装技术
smt生产线需要表面贴装元器件的位置都需要平整,通常焊锡、沉银或者沉金并没有通孔的焊接位置被称为“焊盘”。锡膏,一种由铅锡成分和助焊混合物组成具有粘性的物质,借助锡膏印刷机,渗透过不锈钢或镍制钢网附着到焊盘上,也可通过喷印原理来完成,类似于喷墨打印机。锡膏印刷完毕后,电路板将经过拾取和放置设备,通过相应的传送带进行贴装。将要被贴装的元器件一般放置在纸质或塑料的管道中,并借助飞达安装在SMT贴片机器上。一些个头比较大的集成电路将通过防静电托盘传送。SMT设备从飞达中取出相应的元器件并将其贴装到PCB上,由于PCB上的锡膏具有一定的粘性,因而在焊盘上的元器件有很好的附着效应。
此时,PCB板将被传送至回流焊锡炉中。回流焊先头拥有一个预热区,电路板和元器件的温度逐渐上升,然后进入高温区,锡膏会融化并绑定焊盘和元器件,融化的锡膏表面张力会让元器件保留在所处位置,不发生偏移,甚至该表面张力会自动将略有偏位的元器件拉回到正确位置。回流焊接技术有很多种,一种是使用红外灯(被称为红外回流焊),另一种是使用热气对流,还有一种是最为流行的技术,便是采用特殊的高沸点碳氟化合物液体(被称为蒸汽回流焊)。鉴于环境考虑,这种技术在无铅法规出台后,逐渐放弃。2008年之前,采用标准空气或者氮气对流回流焊是主流。每种方法都有其优劣势。红外照射方式,板设计者必须注意:短元器件不会被高的元件所遮挡,但是如果设计者知道生产过程中使用蒸汽回流焊或者对流回流焊的话,元件位置便不会是需要考虑的因素。在回流焊阶段,一些非常规或者热敏感元器件需要手工焊接,但对于大量的这种元件,就需要通过红外光束或者对流设备来完成相应的回流焊接工艺。
如果PCB板是双面设计,那么所有的锡膏印刷、贴装和回流焊过程需要重复一次,通过锡膏或者红胶将元件粘附在指定位置。如果需要机型波峰焊工艺,元件需要借助红胶进行粘附,以防止元件在波峰焊受热过程中由于焊锡融化而造成的脱落。
完成焊接过程后,板面需要经过清洗,以去除松香助焊剂以及一些锡球,防止他们造成元件之间的短路。松香助焊剂通过碳氟化合物溶剂、高燃点碳氢化合物溶剂或者低燃点溶剂(比如从橙皮中提取的柠檬油精)进行清除。水溶性助焊剂通过离子水和清洁剂清除,然后利用风刀快速移除表面水分。但是,绝大不分的贴装执行无清洗过程,即松香助焊剂将留在PCB板的表面,这将节约清洗成本、提高生产效率、减少浪费。
一些SMT贴装生产标准,比如IPC(Association Connecting Electronics Industries)需要执行清洗标准,以便确保PCB板的清洁,甚至一些无须清理的助焊剂也必须被清除。正确的清晰将清理掉线路之间的肉眼无法识别的助焊剂、脏污和杂质等。但是,并不是所有厂商会严格遵从IPC标准并显示在板面上,或者客户根本不在意。事实上,很多厂家的制作标准是比IPC标准更加的严格。
最后,PCB板需要经过目检,查看是否元件漏贴、方向错误、虚焊、短路等。如果需要,有问题的板需要送至专业的返修台进行维修,比如经过ICT测试或者FCT功能测试环节,直至测试PCB板工作正常。
SMT优势
SMT相比传统的过孔插装技术具有如下主要优势:
(1)更小的元器件。2012年即实现0.4*0.2mm(0.016*0.008 in: 01005),并有更小型化的发展趋势
(2)更高的元件密度(单位面积内的元件数)以及单个元件更多的连接数
(3)更高的连接密度
(4)更低的成本和时间(上线生产)
(5)PCB设计和制作中更少的孔
(6)更加简单快速的贴装
(7)元件贴装中的微小错误会因为融化锡膏的表面张力自动拉伸修复
(8)元件可以在板的上下两面进行贴装焊接
(9)更低的电阻和电感效应,导致更少的RF信号效应
(10)在振动和跌落情况下更好的机械性能
(11)很多SMT元件相比插件元件要更加便宜
(12)更好的EMC性能,鉴于更小的电磁线圈从而产生更低的电磁辐射
SMT劣势
(1)因为更小尺寸和SMD引线间距,贴装或者元件层面的手工维修更加困难,需要专业熟练工人和更贵的返修工具进行操作
(2)SMD元件不能直接用于插入式母板(一种快速测试打样工具),需要定制一块PCB或者将SMD元件焊接到引脚载具上。
(3)SMD焊锡连接可能在热力循环中被灌注成分损坏
(4)SMT焊接连接处变得更小,间距越来越小,导致SMT工艺要求精度更高
(5)SMT不适于大体积、高能、高电压元件,例如电源电路中的变压器等,将SMT和插件工艺融合在一起,是比较常见的。
(6)SMT不适用于频繁机械应力的应用中,比如一些连接器,作为接口同外部连接,频发拔插对于焊接的稳定性提出了挑战
SMT返修
SMT贴片加工维修在整个PCBA加工工艺过程中,SMT问题元件经常采用电烙铁或者非接触式返修系统进行维修。在通常情况下,返修系统是更好的选择,因为SMD元件的维修需要相当熟练技能,并且不太容易。非接触式焊接返修方法:红外焊接和热气焊接。
红外方式
通过红外焊接方式,焊接处经过长短波的电磁感应而受热融化。优势有:
(1)建议安装
(2)无须加压空气
(3)无须针对不同元件的吸嘴,减少更换吸嘴的成本
(4)快速红外源的反应
劣势
(1)中央区域相比外围区域受热更多
(2)温度控制不够精确,极易达到峰值
(3)周围元件需要覆盖,避免损害,需要更多的时间
(4)表面温度取决于元件的反射率
(5)温度取决于表面形状,对流能量损耗将减少元件的温度
(6)没有回流氛围可能性
热气方式
在热气方式的焊接中,连接处的能量受热通过热气传输,通常借助空气或者氮气。优势
(1)模仿回流焊接中的场景
(2)一些系统允许在热空气和氮气中进行切换
(3)标准元件吸嘴,拥有更高的稳定性和快速处理过程
(4)允许可再生焊接
(5)足够的热能,大量元件均可以受热
(6)受热均匀
(7)元件受热温度不会超过设定的气体温度
(8)回流之后的快速冷却,导致更小的焊接纹路
劣势:热发生器的热力性能导致较慢的反应。返修通常能够更正一些由于人工或者机器引致的错误,包含如下步骤
融化焊锡并且移动元件
移动残余焊锡
直接或分发式印刷锡膏在PCB板上
贴装新的元件并回流焊
一些情况下,成百上千个相同的元件需要维修。这种错误经常在贴装过程中发生并被捕获。但是,当发现过晚时,就要面临大批量的维修,此时需要有针对性的维修策略,确保维修的品质。
江西英特丽电子科技有限公司成立于2016年5月,坐落于人杰地灵的才子之乡-江西省抚州市临川区,江西英特丽电子科技有限公司现有30,000平方米的厂房面积,24条SMT产线,8条插件线,4条波峰焊线,8条组装线,4条包装线,总投资10个亿,配备先进完善的数字化管理体系,致力于打造工业4.0智慧工厂。
上一篇: 英特丽SMT贴片加工中工艺质量的控制 下一篇: 英特丽PCBA加工好的产品保存期限有多久
Copyright © 2020-2022 赣ICP备19014000号-1
赣公网安备36100002000168号 江西英特丽电子科技股份有限公司深圳分公司
